End-of-Line-Prüfung: Sichere Batterien für Elektrofahrzeuge
Anbieter zum Thema
Von der einwandfreien Funktionsweise der Batterien hängt die Reputation der Hersteller von Elektrofahrzeugen ab. Daher hat Hahn Automation Group einen Batterietester entwickelt, der automatisiert eine 100%-Prüfung der mobilen Energiespeicher durchführt. An zentraler Stelle: ein 3-Achs-Portal für die optische und Dichtheitsprüfung, bestehend aus elektrischen Antrieben von Festo.
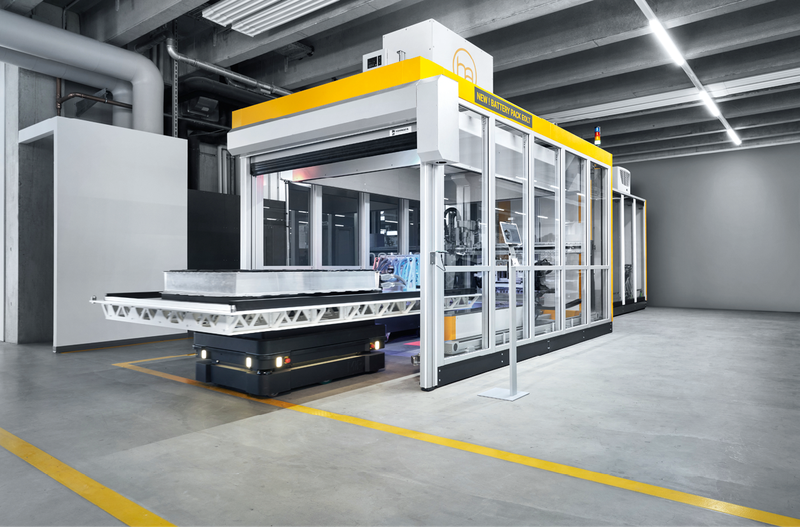
Der Hahn Battery EOLT ist eine Komplettlösung zum Prüfen von Batteriepacks. Auf dem End-of-Line-Testsystem können alle relevanten Testszenarien für 90 Prozent aller am Markt verfügbaren Batteriepacks umgesetzt werden, denn die Anlage ist auf viele Größen einfach skalierbar. Von der Leistungselektronik über Prüfgeräte bis hin zur Prüfsoftware und Automatisierung bietet Hahn Automation Group alles aus einer Hand. „Dank des großen Fachwissens in Sachen Prüftechnik hilft das Unternehmen, die besten Strategien für die End-of-Line-Prüfung zu definieren, um Zykluszeiten zu optimieren und die angestrebte Produktqualität zu gewährleisten“, sagt Christian Bubat, Global Business Development Manager bei Hahn Automation Group. Bei der Entwicklung arbeitete das Unternehmen mit dem Lehrstuhl „Production Engineering of E-Mobility Components“ (PEM) der RWTH Aachen zusammen.
Auf Nummer sicher bei der End-of-Line-Prüfung
„Ein neu entwickeltes Brandschutz- und Sicherheitskonzept für den Batterietester EOLT stellt im Falle eines Brandes dessen zuverlässige Erkennung sicher“, ergänzt Martin Sulzbacher, Leiter R&D bei Hahn Automation Group. In einem solchen Fall wird die Batterie vollautomatisch verschlossen, um den Brand einzudämmen, und anschließend ebenfalls vollautomatisch in einen sicheren Bereich transportiert. Rauchfilter verhindern die Kontaminierung der Umgebung. „Brände in Batteriefabriken haben mitunter zu zwei Wochen Produktionsstopp geführt, denn die Hallen mussten aufgrund der giftigen Dämpfe aufwändig gereinigt und dekontaminiert werden“, so Sulzbacher weiter.
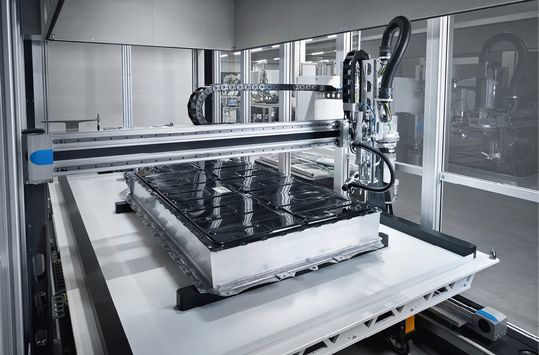
Jeder Schritt automatisiert
Soweit das Sicherheitskonzept. Doch wie läuft ein Batterietest ab? „Wir wären nicht Hahn Automation Group, wenn wir nichts unversucht ließen, jeden Prozessschritt zu automatisieren“, so Bubat weiter. In einem ersten Schritt fährt ein Batteriepack mit einem selbst fahrenden AGV in den Batterietester ein. Über eine eigens entwickelte, standardisierte Kupplung wird das Batteriepack mit Steckern kontaktiert, dabei geladen und wieder entladen. Ein Hochvolttest ergänzt die elektrische Testroutine. Um die Dichtigkeit eines Batteriepacks zu prüfen, wird dieser mit Helium befüllt.
Am 3-Achs-Portal mit den elektrischen Antrieben vom Typ EGC von Festo ist eine Helium-Schnüffellanze für den Dichtigkeitstest sowie eine Kamera für die optische Prüfung angebracht. Angetrieben werden die Achsen von den Motoren EMMT-AS und angesteuert von den Controllern CMMT-AS von Festo. Damit ist das Antriebs- und Steuerungspaket passend aufeinander abgestimmt.
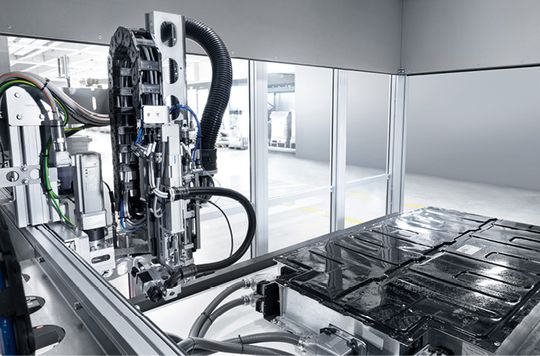
Mehrere Prüfungen zusammengefasst
Das Achsportal bewegt und positioniert diese beiden Sensoren entlang aller Kanten des Batteriepacks, um eventuelle Leckagen am Gehäuse und am Kühlsystem der Batterie aufzuspüren. Die Kamera prüft den korrekten Sitz aller Schilder und Aufkleber sowie die einwandfreie Verarbeitung des Batteriepacks und spürt eventuelle mechanische Schäden auf. Ein Test des Batterie-Management-Systems überprüft die Kommunikation und bewertet die Sensoren.
„Wie die einzelnen Prozessschritte zeigen, betrachten wir das Thema Batterieprüfung aus dem Blickwinkel der Automatisierung. Der Batterietester fasst mehrere Prüfungen zusammen und könnte dreischichtig 24 Stunden in Betrieb sein“, erklärt Bubat. Daher sei es wichtig, dass Hahn Automation Group auch auf Lieferantenseite mit verlässlichen Automatisierungspartnern zusammenarbeiten könne, die die Aufgaben und Ziele von Hahn Automation Group verstünden, so Bubat weiter.
End-of-Line-Prüfung: Schnelle Auslegung und Simulation
„Wie schon in vielen vorangegangenen Automatisierungsprojekten hat sich gezeigt, dass Festo der richtige, weltweit verlässliche Partner in der elektrischen und pneumatischen Automatisierungstechnik ist“, ergänzt Sulzbacher. Dabei beginnt die Partnerschaft mit Festo schon bei der Konstruktion und Produktauswahl: „Einfach zu bedienende Auslegungs- und Simulationstools erleichtern uns die Arbeit“, fährt er fort. Durch die langjährige Partnerschaft kennt man die Automatisierungsprodukte von Festo schon lange und kann sie gezielt einsetzen. Mit Online-Produktfindern, intelligenter Auslegungssoftware und den Engineering-Tools finden die Konstrukteure von Hahn Automation Group ohne aufwendige Berechnungen die passenden Produkte für die Entwicklung neuer Maschinen und Anlagen.
Der Autor Christopher Haug ist Manager International Trade Press bei Festo.
Lesen Sie auch: Antriebslösungen und Digitalisierung: Die große Expertenumfrage